Continuous Polyester Plants
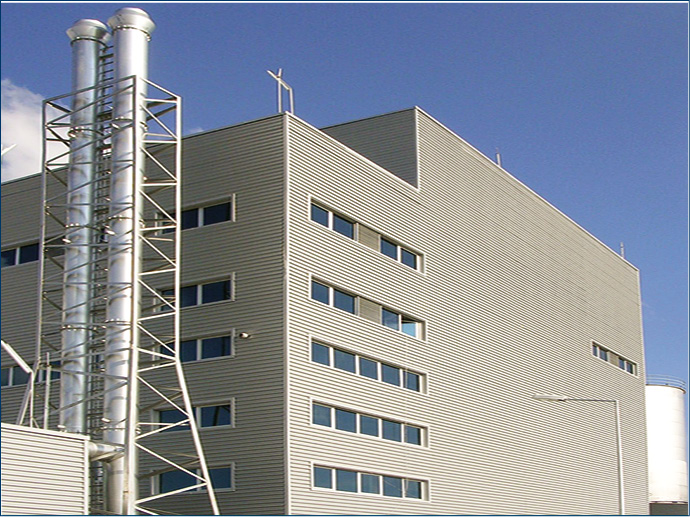
AQUAFIL Engineering has long experiences in building and designing continuous and batch polycondensation plants for textile, film and bottle grades. Some of our engineers are working in the business field already more than 40 years. Wolf Karasiak, the founder and former managing director of AQUAFIL Engineering is the inventor inventor of the shaft less finisher DRC®(called Disc-Ring-Cage reactor). The finisher design has been upgraded in the last years and is used now for medium viscosities as well as for high viscosities up to IV 1.2.
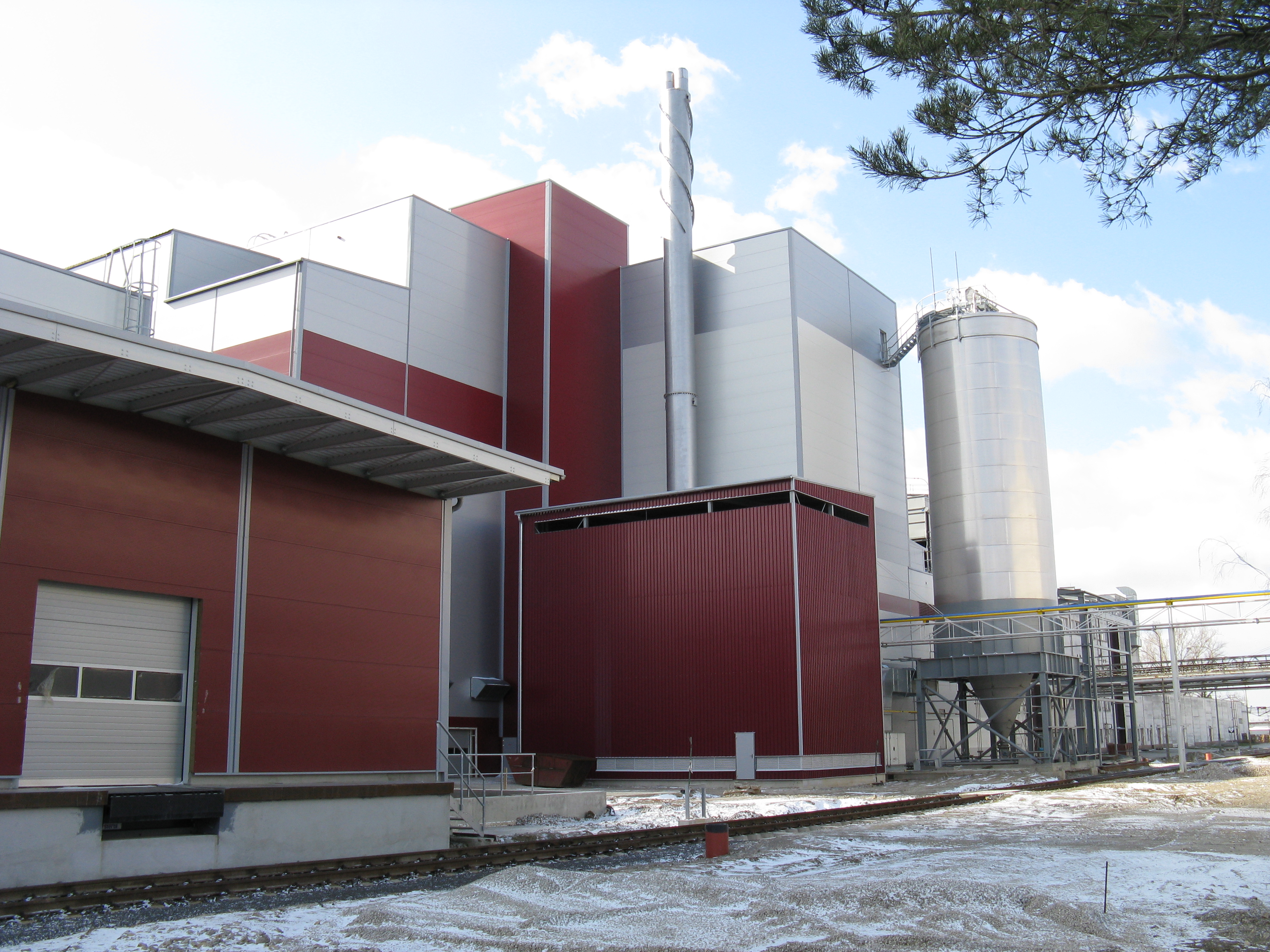
2-Reactor Technology
The 2-Reactor plant technology can be used for capacities up to 600 tons/day. AQUAFIL Engineering analyzed carefully the market situation in the past. The study showed the request of the market and the customers for highly efficient plants and low conversion costs. Even if all competitors were following the way of large production scales to reduce the operating costs, AQUAFIL Engineering was working on a different strategic approach.
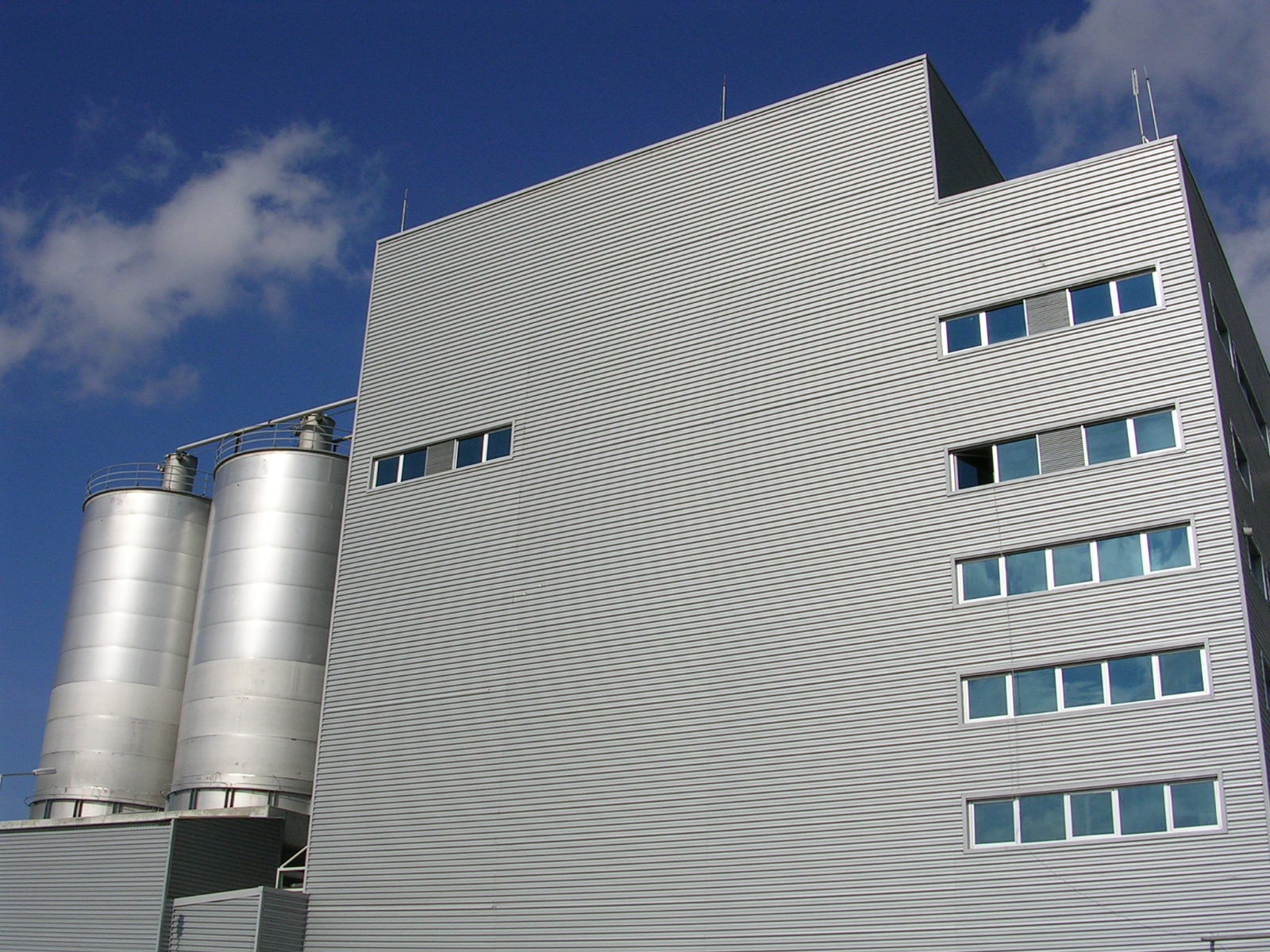
Small is in, Large is out.
Following the idea of smaller, more flexible and simplified production AQUAFIL Engineering has designed a 2-Reactor process for which patents have been granted for the technology as well as for the equipment. The concept of simplified and flexible polycondensation plants allow to compete with the production cost of large scale plants. The 2-Reactor technology based on the unique AQUAFIL UPR®(Universal Polymerisation Reactor) can be used for textile-, film- and bottle applications with IV 0.58-0.68 and technical yarns with IV up to 0.98.
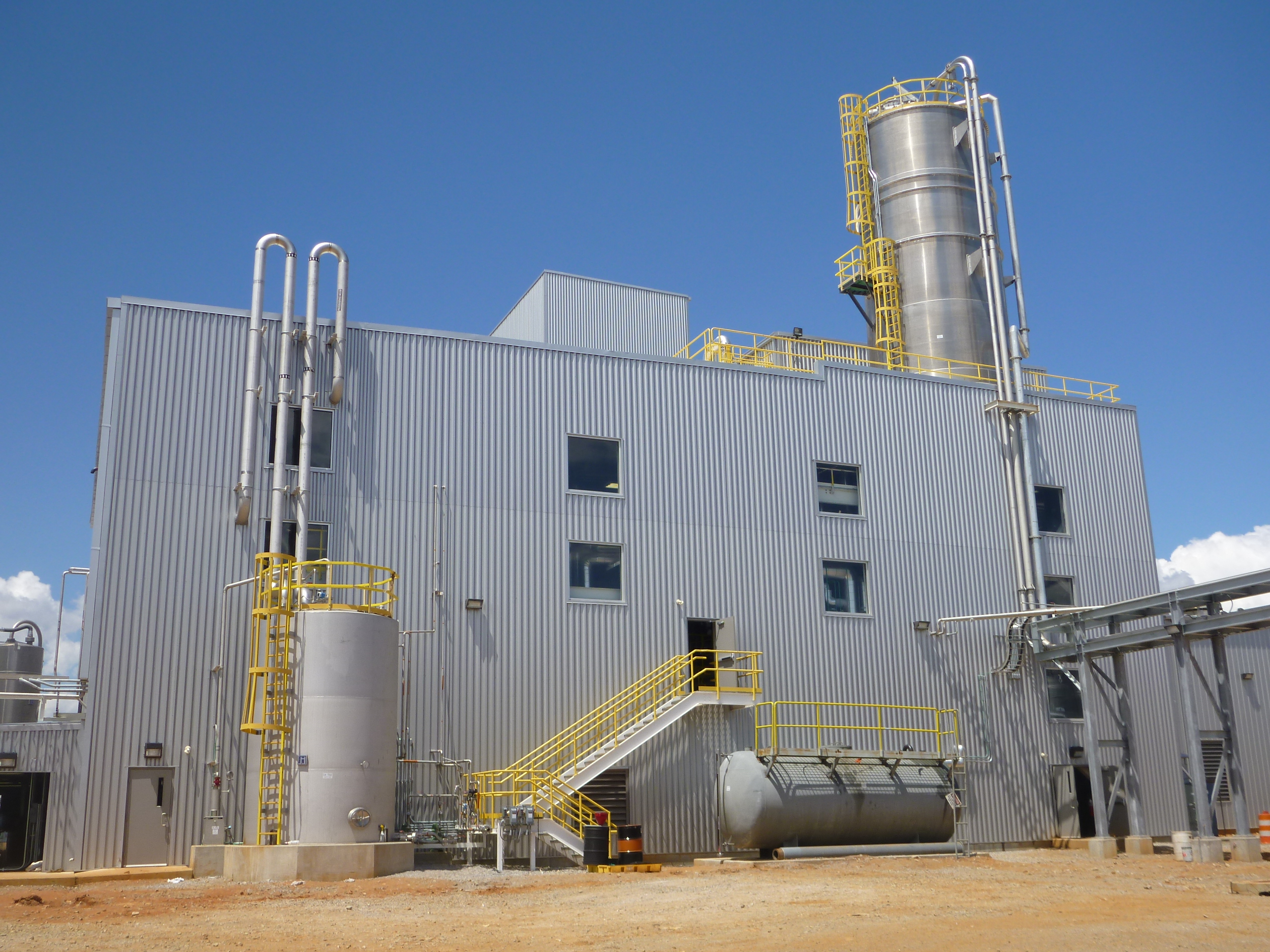
LBT® - Low Building Technology
The newest development of AQUAFIL Engineering is the LBT® polycondensation plant. It fits into a simple storage hall and does not require a difficult building structure. Customers can drastically reduce the building and erection cost and time, up to 50%. Additionally, the LBT® plants achieve the lowest electrical consumption worldwide compared to latest competitor plants.
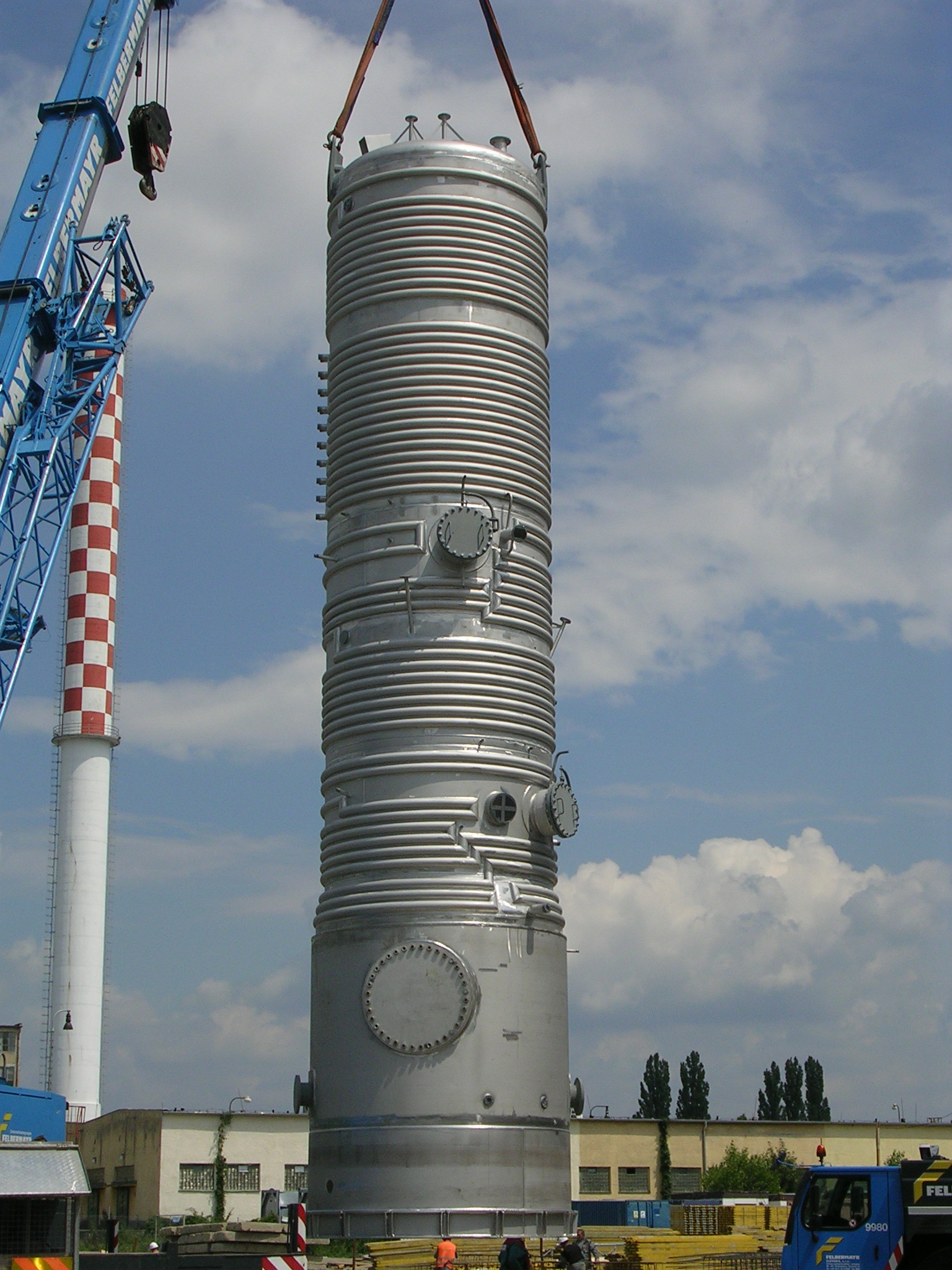
LBT® and UPR® Advantages
- less equipment cost
- less utility consumption
- shorter hold-up and reaction time
- lower AA-generation
- lower DEG formation due to large surfaces, low temperatures
- lower oligomer formation and losses
- reduced space and building cost
- shorter project realization time
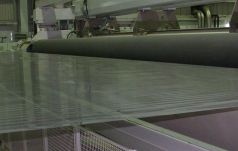
DFC® - Direct Film Casting
The direct film casting (DFC®) technology of AQUAFIL Engineering connects directly the polycondensation plant with the film production line. The polymer melt is transported via pipe to the die head of the film line (BOPET or CAST). As the DFC® is avoiding the crystallization, drying and remelting of the polyester chips in the film line, it is saving a lot of investment, space and operation cost. Additionally the product quality and run ability make a remarkable step upwards in the final film product.
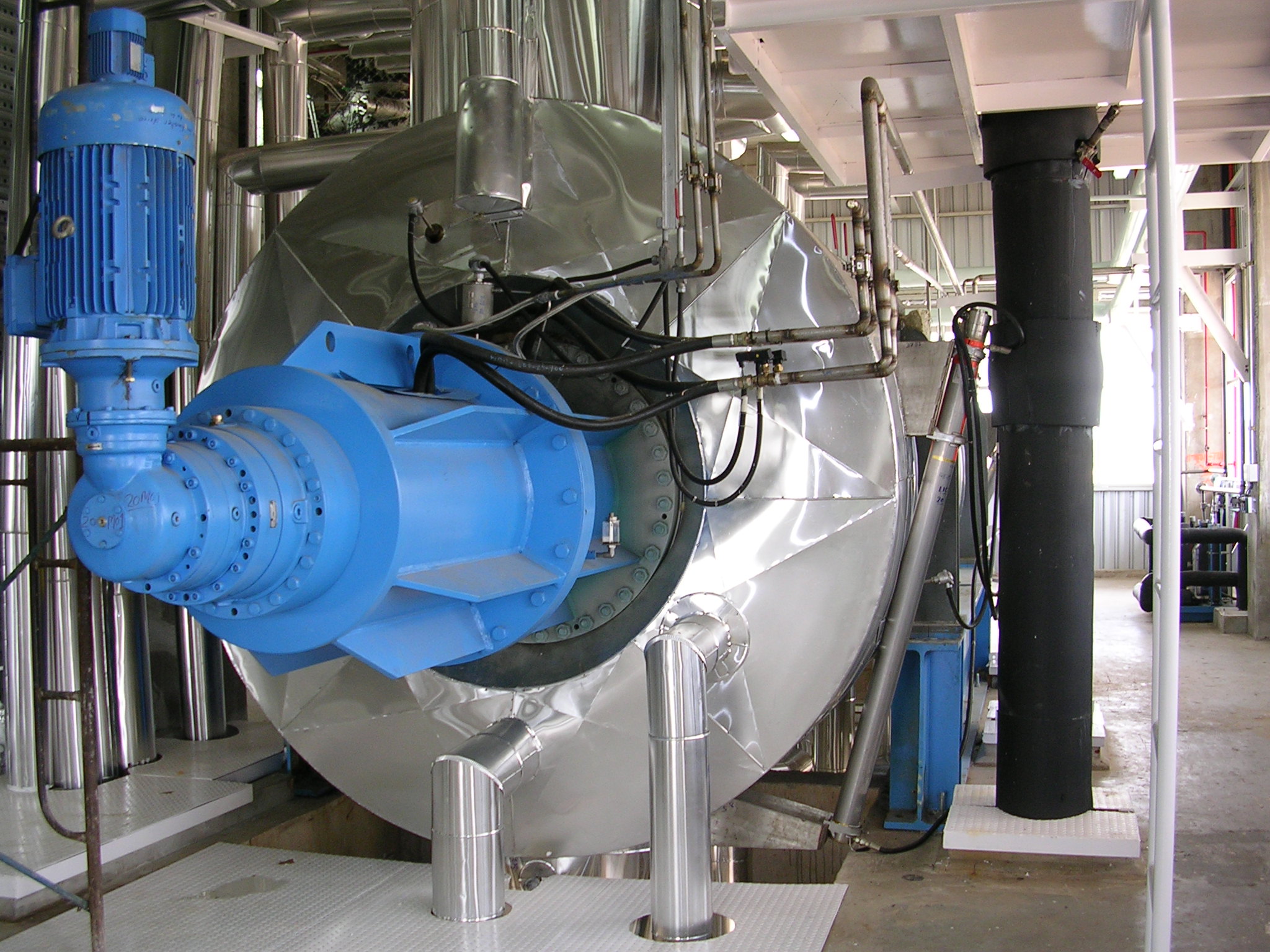
Polyester Process and Reactor
The unique reactors of the polyester process are designed and patented by Aquafil Engineering. The reactors are fabricated by selected manufacturers with high quality standards in Europe.
Before the main reactors are shipped to the clients of AQUAFIL Engineering, each reactor is tested with a heat and vacuum test according to AE standards in the workshop.
Melt to Fiber/Resin/Preform/Film Process
AQUAFIL Engineering can supply polycondensation plants for direct spinning of fibre or filaments (DSP), direct film casting (DFC®) and high viscosity for resin.
Modifications needed for fiber, resin or film applications can be made with special AQUAFIL Engineering Melt Modifying Systems (MMS).